We have a stringent approach to process safety to make sure our facilities are well designed, well operated and well maintained, so they can run safely and without harm to people or the environment. The global safety standards we apply to all the facilities and projects we operate meet local regulatory requirements, and in many cases exceed them. Since 2006, Shell has been implementing a $6 billion programme to improve the safety of our oil and gas production facilities, including regular training for those who manage and operate them. In 2012, we invested around $1 billion in the safety and reliability of our refineries, chemical plants and distribution facilities.
Shell takes a dual approach to potential incidents. We identify and assess risks that have the potential to become an incident, and take the necessary steps to reduce or eliminate them. At the same time, we prepare for, and are ready to respond to, an incident in the event that one occurs.
We learn from investigations into major industry incidents. Shell has a programme in place to improve awareness among managers of how they can better create a working culture that prevents safety incidents. This includes recognising and responding to the smallest signs of a potential problem. It also includes asking workers more questions about their safety concerns.
We routinely prepare and practise our emergency response to incidents such as an oil spill or a fire. We work closely with local emergency response crews and government organisations to regularly test our plans and procedures, with the aim of continually improving our readiness to respond. If an incident does occur, we have multiple recovery measures in place to minimise the impact on people and the environment.
Opinion
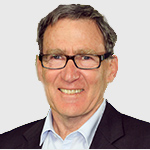
I have run numerous process safety workshops for Shell, and I am struck by the way the company has tried to learn the process safety lessons that have emerged from previous disasters. It has identified 11 “process safety basic requirements” (PSBRs). They are summarised on a single card, and the requirements refer to things like safe siting of portable buildings, permit to work and alarm management. Each of these is linked to specific industry incidents. This linkage is what breathes life and meaning into the PSBRs. They are not just abstract procedures: they are the result of the hard lessons of previous tragedies. The PSBRs represent organisational learning. The next step is to ensure that people know and can tell the stories of the incidents from which the PSBRs are derived. In this way organisational learning will be translated into individual learning.”
Andrew Hopkins
Emeritus Professor of Sociology at the Australian National University, Canberra, Australia