million tonnes
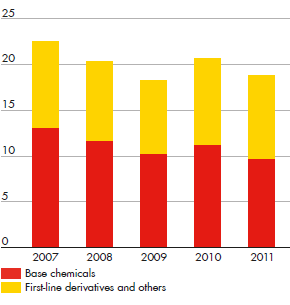
[A] Excludes volumes sold by equity-accounted
investments, chemical feedstock trading and
by-products.
We produce and sell petrochemicals to some 1,100 major industrial customers worldwide, with the top 20 customers accounting for about 42% of our third-party sales proceeds. Our range of petrochemicals includes base chemicals, such as ethylene, propylene and aromatics; and first-line derivatives, such as styrene monomer, propylene oxide, solvents, detergent alcohols, and ethylene oxide. Our customers, many of them leading companies in their own fields, use these products to make everyday items, such as plastics, detergents, textiles, medical equipment and computers. All in all, we sold almost 19 million tonnes of bulk petrochemicals in 2011.
We also produce additives for fuel and lubricants, and catalysts for refinery and petrochemical markets. Shell catalysts have steadily improved the production of ethylene oxide, an important building block for synthetic fabrics, plastic bottles and antifreeze. More efficient ethylene oxide production has the benefit of lowering CO2 emissions.
Shell petrochemical alcohols are the basis of more concentrated household laundry detergents that clean clothes at lower temperatures. Compared with traditional powders, they not only require less detergent per wash but also have lower packaging, shipping-weight and shelf space requirements. Washing laundry at colder temperatures can help consumers to save energy.
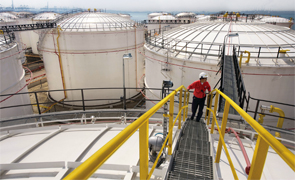
MEG storage and facility at the Shell
Eastern Petrochemicals Complex (SEPC),
Singapore.
Over many decades we have developed the proprietary technologies, processes and catalysts that enable Shell to enjoy a powerful competitive advantage in our core petrochemical markets. Our OMEGA technology is considered the most efficient technology currently available in the world for converting ethylene to ethylene oxide, which is used to make a wide range of industrial and consumer products, such as polyester films and fibres, engine coolants and antifreeze. OMEGA uses about 20% less steam and 30% less waste water than a traditional thermal conversion MEG plant with the same capacity. The technology also produces significantly less carbon dioxide per tonne of MEG than conventional processes.
In Singapore, we are building a demonstration unit to manufacture the chemical ingredient diphenyl carbonate, a versatile and growing engineering plastic used in a wide variety of applications, from optical media, household items, automotive components to electronics and sheeting/film.
We will continue to focus on the synergies among our chemical plants, refineries and Upstream businesses to increase the supply of the best available feedstock for our crackers.
Our Chemicals strategy is based on selective growth at existing sites through increases in capacity, improvements in efficiency and integration, and strengthening our feedstock sources. It is also based on securing integrated growth projects with partners and developing technologies to convert gas to chemicals.
In 2011 we signed a heads of agreement with Qatar Petroleum for the joint development of a proposed major petrochemical complex whose feedstock would come from natural gas projects in Qatar. We are working with the Qataris and Petrochina to develop a potential integrated refinery and petrochemicals complex in China. We are also developing plans to build a proposed world-scale ethylene cracker with integrated polyethylene derivative units in the Appalachian region in the North East of the USA.