Contractors and suppliers
Shell aims to work with contractors and suppliers that behave in an economically, environmentally and socially responsible way, as set out in our Shell General Business Principles. The Shell Supplier Principles cover our requirements for suppliers in business integrity, health and safety, social performance and labour and human rights.
In 2017, Shell spent $42.2 billion on goods and services from 33,505 suppliers globally.
Suppliers who work to deliver Shell projects and help run our operations are invited to register with our supplier qualification system (SQS). Certain areas of our supply chain may pose a higher risk to labour rights due to their location and the nature of the goods and services we procure. In these cases, we use a defined set of criteria to identify potential supply chain risks and, where we see risk, we ask suppliers to undertake due diligence assessments prior to the award of a contract. We require our suppliers to declare whether they have a process in place to assess and manage social risks with their own suppliers.
If gaps are identified, we may work with suppliers and contractors to help them understand how to close these gaps, implement corrective action – which may include on-site audits from Shell – or we may consider terminating the contract.
This risk-based approach is shared in several external regulatory declarations that describe how we manage human rights risks in our supply chains, most recently in our statement under Section 54 of the UK Modern Slavery Act 2015.
Applying risk filters
When we assess our suppliers, we use a combination of the type of work they do and the country in which the work will be delivered to identify suppliers we consider high risk for potential labour rights violations.
Labour rights risk analysis 2017
Results and working with suppliers to close gaps
The results of our supplier assessments are summarised in a green/amber/red rating depending on the number and significance of any gaps between our requirements and the supplier’s policies or performance.
We engage with each supplier that has serious gaps to ensure they have a correction plan. The most common gaps found during our supplier assessments, which typically relate to policy rather than performance gaps, are:
- freely chosen employment;
- child labour avoidance;
- working hours, wages and benefits;
- dormitory, housing and working conditions;
- humane treatment, equal opportunities and freedom of association; and
- supply chain and performance management.
Contractor safety leadership
We share our safety experience and standards with other operators, contractors and professional organisations, including the International Association of Oil & Gas Producers (IOGP). For more details on how we helped raise industry standards in 2017, see the Safety section.
Shell Ariba Procurement: SHARP
We have adopted a new contracting and procurement platform to make it as easy and smooth as possible to do business with Shell. SAP Ariba, a market standard solution, has replaced some of our IT systems and will be known as Shell Ariba Procurement, or SHARP. It enables us to process procurement data more efficiently, reduce costs and track purchase orders and invoices in real time. For more details on ways Shell Ariba Procurement is improving our supply chain see www.shell.com
SHARP also helps suppliers easily take part in online sourcing or tenders and provide their web catalogues for Shell employees wishing to place orders. View our website (www.shell.com/aribaprocurement) to get a supplier’s perspective on what it has meant to them to join SAP Ariba.
Care for people
Good working and living conditions help to bring about a safer and more productive working environment. Our approach to worker welfare means supporting the needs of the individual worker, their relationship with their family and connections with colleagues. We aim to provide a home away from home for people by delivering a standard of accommodation and facilities that improves their quality of life and well-being, and as a result promotes safe and productive work.
In Shell contracts, suppliers agree to provide and maintain safe and healthy working conditions for all supplier personnel. In 2017, we ran a series of engagements with Shell procurement teams in higher-risk locations to raise awareness and improve understanding of contractor worker welfare. For some services in these locations, we also require contractors to develop a worker welfare plan that includes ethical recruitment practices and no use of forced labour. In our Singapore operations, for example, an opportunity was identified for our contractors to improve on-site and off-site welfare of workers, as well as clarify worker recruitment practices. An element of this included building awareness of worker welfare and the correlation to increased performance in safety, productivity, quality and retention with government and local industry bodies. Several changes have been made, including in on-site and off-site infrastructure, fatigue management, and transport, all done with a strong voice from the workers themselves.
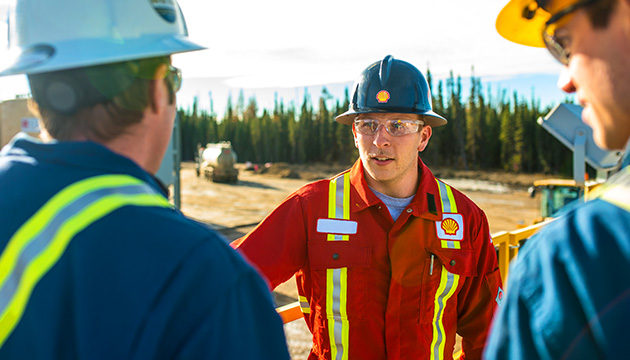
We engage with each of our suppliers that have serious gaps in their policies or performance to ensure they have a correction plan.