Contractors and suppliers
In 2016, Shell spent $45 billion on goods and services from 43,000 suppliers globally.
Shell aims to work with contractors and suppliers that behave in an economically, environmentally and socially responsible way, as stated in our Shell General Business Principles. The Shell Supplier Principles cover what is required from our suppliers regarding business integrity, health and safety, social performance, and labour and human rights.
Assessing our suppliers
Certain areas of our supply chain may pose a higher risk to labour rights due to their location and the nature of the goods and services we procure. In these cases, we use a defined set of criteria to identify potential supply chain risks and, where we see risk, we ask suppliers to undertake due diligence studies before considering awarding a contract. A successful example of this is the retailer Abenson Ventures in the Philippines (see external opinion). In 2016, 1,436 suppliers who worked to deliver Shell projects and help run our operations, were required to register with our Supplier Qualification System (SQS). Of these suppliers, several hundred were flagged for second stage qualification for one of our risk filters, 70 of which were flagged for labour risks analysis (see the infographic below for further detailed analysis).
Applying risk filters
When we assess our suppliers, we use a combination of the type of work they do and the country in which the work will be delivered to identify suppliers we consider "high-risk" for potential labour rights violations.
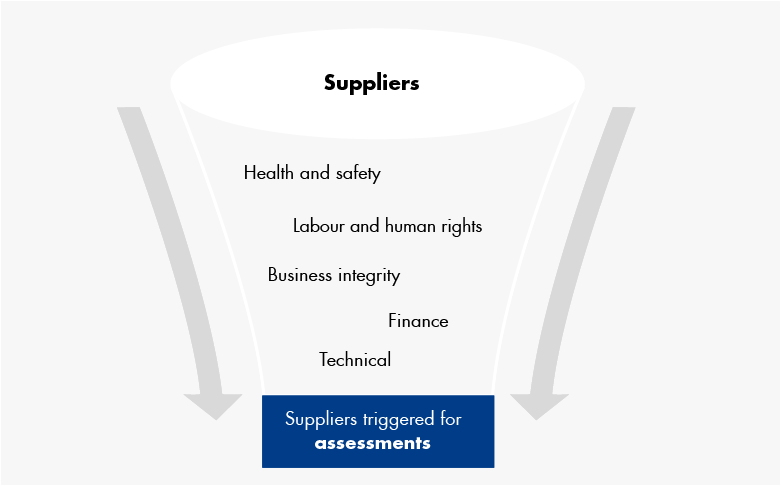
Applying our labour rights risk criteria during our sourcing process in 2016, we identified and assessed 70 high-risk suppliers. Of those, 23 were awarded contracts.
Labour rights risk analysis 2016

Labour rights risk analysis 2016
The results of our supplier assessments are summarised in a green/amber/red rating depending on the number and significance of any gaps between our requirements and the supplier’s policies or performance.
We work with each of these suppliers to ensure they have a plan to correct serious gaps. These are the most common gaps found during our supplier assessments, which typically relate to policy rather than performance gaps.
- freely chosen employment;
- child labour avoidance;
- working hours, wages and benefits;
- dormitory, housing and working conditions;
- equal opportunities and freedom of association; and
- supply chain and performance management.
Contractor Safety Leadership
Senior leaders from Shell and 14 contractors developed the Contractor Safety Leadership Initiative Declared Future. This outlines a joint vision for safety leadership with the ambition of no harm and no leaks achieved through collaboration.
Performance can be improved by aligning the health, safety, security and environment (HSSE) frameworks of a contractor and Shell, by empowering the contractor to deliver using their own HSSE controls and by visiting sites together to listen to the workforce. Teams are encouraged to jointly attend talks, conduct risk assessments and oversee the completion of projects.
Local supplier development
Shell aims to contribute to the economic development of countries where we operate through employment and by helping local companies develop, either by employing people directly or through our government and business partners. At the start of a project, as well as throughout the project life cycle, we consider how we can employ local suppliers and use community knowledge. If needed, we help them build capabilities that meet our safety and quality standards. We also support the growth of local businesses in many countries where we work. In many countries, a plan to support the growth of local businesses forms part of the selection criteria against which potential suppliers are assessed.
For example, Qatar Shell spends more than 50% of its annual procurement budget with local companies. Fourteen contracts have been awarded to small- and medium-sized local companies since 2013 (with six awarded in 2016) worth around $19 million.
External opinion
“As a retailer, we supply corporate merchandise to companies like Shell. Their Supplier Qualification System (SQS) helps us align our policies to the international standards Shell expects. It is important we provide stakeholders with clear policies that improve our way of doing business. We take pride in providing our customers with the best products and services, which would not be possible without a sophisticated platform designed for suppliers, like SQS.
We have several business units in the Philippines and SQS enables us to standardise and streamline the way we engage with Shell companies in different locations. We expect this will reduce costs, time and avoid duplication of effort. We are delighted that improving our policies merits a green banding.”
“We expect to reduce cost and time”
CJ Barrion
Abenson, Philippines