Process safety
Process safety management is about keeping hazardous substances in pipes, tanks and vessels so they do not cause harm to people or the environment.
It starts with designing and building projects and is implemented throughout the life cycle of the facilities to ensure they are operated safely, well maintained and regularly inspected.
Refreshing our approach
Process safety management remains central to the updated approach to safety we started to deploy for all employees and contractors from 2020 (see Our approach to safety).
While we continue to work to prevent incidents through maintaining safety barriers and ensuring good operating practices, we are also implementing our refreshed approach which has a more consistent focus on how people interact with these processes. We acknowledge that people can make mistakes and processes can fail.
We are working to ensure continuous learning is a deeply embedded habit and our workplace is an environment where people feel comfortable to speak up, particularly on difficult issues.
We are updating the various systems and controls we have in place to enable people to more effectively identify and address potential safety incidents. For example, we are improving work planning by having more in-depth discussions before, during and after tasks to identify and implement improvements.
Increasingly, we concentrate on leading indicators of process safety to understand the effectiveness of our barriers and work processes, rather than focusing just on indicators of past performance, such as the absence of safety incidents.
Risk management approach
Our global standards and operating procedures define the controls and physical barriers we believe are necessary to prevent incidents. We refer to this system of barriers and recovery measures as a bow-tie model, which visually represents a system where process safety hazards are managed through prevention and response barriers.
We also continue to better align the various approaches to managing facilities across our businesses to enable safer ways of working. For example, all Shell-operated facilities and some non-operated ventures have adopted a single global asset management system. The system simplifies work processes and helps people across Shell share expertise in asset equipment care, maintenance, learning from incidents and assurance.
Process safety fundamentals
Our refreshed approach to safety is built on work we have carried out since 2016 to strengthen barriers involving critical safety tasks performed by front-line staff. Embedding a set of 10 process safety fundamentals across Shell has been key to this approach. They provide clear guidelines for good operating practice to prevent unplanned releases of hazardous materials. We encourage employees and contractors to use them in daily conversations to identify safety dilemmas, so they can be resolved.
Advances in technology
In 2020, we increased our use of drones, robots and digital technology, such as augmented reality, as lockdowns caused by the COVID-19 pandemic disrupted the movement of people. This technology enabled us to carry out more remote monitoring and continue to assure data to meet safety and environmental performance reporting standards.
An example of this technology in action is at the Shell-operated Ormen Lange facility where teams sent a remote-controlled vessel alone into the Norwegian Sea, 100 kilometres from land, to inspect the gas field. This enabled mariners based in Ireland to take the helm using a computer-generated joystick without breaching COVID-19 restrictions. Read the full story: How technology stepped up when COVID-19 struck at www.shell.com/inside-energy
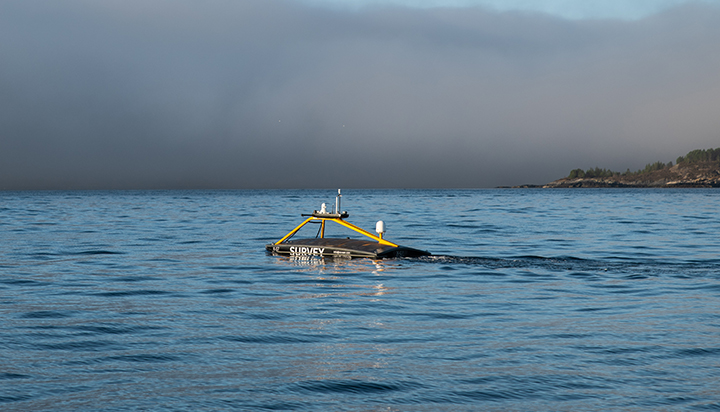
The X-07 vessel collected data from the Ormen Lange gas field in Norway, while remotely operated by experts based in Ireland.
Process safety performance
In line with industry standards, we measure and report process safety incidents according to significance, with Tier 1 as the most significant category.
Tier 1+2 operational process safety events [A]
* excluding sabotage
[A] Process safety events classified according to guidance from the IOGP and API. In 2020, there was one Tier 1 sabotage-related event. The classification of sabotage-related process safety events is made on the best-endeavours basis.
The number of Tier 1 and 2 operational process safety events decreased from 130 in 2019 to 103 in 2020, of which 34 were Tier 1 and 69 were Tier 2. For comparison, there were 41 Tier 1 and 89 Tier 2 operational process safety events in 2019. This is Shell’s best annual performance for combined Tier 1 and Tier 2 incidents since implementing this industry process safety performance metric.
In 2020, there was one significant process safety incident related to a fire and subsequent equipment damage in the Shales business in Texas. The fire was caused by mechanical failure of a pump that caused a release of lubrication oil that caught fire and damaged several pumps. There were no injuries associated with this event.
Process safety events related to sabotage and theft in Nigeria are recorded separately. There was one Tier 1 event in 2020 compared with nine in 2019.
Visit www.shell.com/safety for more on Shell and safety.
Visit www.shell.com/process-safety for more on our approach to process safety and full details of our approach to risk management, including the controls and physical barriers we believe are necessary to prevent incidents.