In Focus: Pearl GTL
The Pearl gas-to-liquids (GTL) plant in Qatar is an example of a large and innovative Shell project. Pearl GTL, the world’s largest GTL plant, is based on proven and proprietary Shell GTL technology. It maximises value from offshore gas production, onshore gas processing and the refining of premium products, which we sell globally.
Key facts
- Location: Qatar, Ras Laffan Industrial City
- Ownership: Development and Production Sharing Agreement (DPSA) with the State of Qatar; 100% Shell funding
- Peak production: 1.6 bcf/d of wellhead gas resulting in:
- 140 thousand b/d of GTL products (two trains) – gas oil, naphtha, kerosene, paraffin and lubricants base oils
- 120 thousand b/d of ethane, liquefied petroleum gas (LPG) and condensate
Upstream, the project produces gas from the world’s largest single non-associated gas field, the North Field. The offshore scope includes 22 production wells, two unmanned wellhead platforms in about 30 metres of water and two 30-inch pipelines running about 60 kilometres (km) to shore.
In Qatar, summer temperatures exceed 40°C (104°F) and rainfall is very low. Conserving water is critical. Pearl GTL was designed to be self-sufficient in its use of water. The industrial water processing plant is the world’s largest, recovering, treating and reusing all the industrial process water nearly all the time. With a capacity to treat 280,000 barrels of water a day, Pearl GTL’s water treatment plant is comparable to that for a city of 140,000 people.
Shell funded 100% of the development costs of Pearl GTL under a profit-sharing agreement with the State of Qatar.
Before Pearl GTL, the industry considered completing a production well in the North Field in 75 days to be a good performance. The project used a novel system called simultaneous operations – a technique where two wells were worked on at the same time – getting one well ready to produce while drilling the next, resulting in some of the shortest String Time per Well times ever recorded in the North Field. Using this technique, 22 wells were completed in an average of 45 days. The fastest well completion took just 28 days. A total distance of 97 km was drilled in the rock below the seabed, constructing wells containing enough steel to build two-and-a-half Eiffel Towers. The drilling crew saved a total of more than 600 days’ drilling time.
Shell GTL technology has been developed over more than four decades. The proprietary Shell Middle Distillate Synthesis (SMDS) process is at the heart of the two-train Pearl GTL plant. It is underpinned by more than 3,500 patents and – above all – was proven on a commercial scale during more than 10 years of operations at Shell’s first GTL plant in Bintulu, Malaysia, which has a capacity of 14,700 barrels per day (b/d).
Shell is the first to commercially produce lubricants from natural gas. GTL products produced by Shell include GTL base oil, GTL naphtha, GTL kerosene, GTL gasoil, GTL normal paraffin, GTL waxes as well as other specialties such as drilling fluids and hydrocarbon solvents. Shell premium quality passenger car motor oils made from GTL base oil are now available in over 100 markets around the world.
Shell GTL Fuel, made from GTL gasoil, is a cleaner-burning alternative to diesel fuel that helps reduce local emissions and thereby improve local air quality. It is available to customers in Europe.
How GTL base oils are produced using GTL technology, marketed as Shell PurePlus Technology
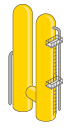
1 Gasification
Methane from natural gas reacts with pure oxygen to produce synthesis gas
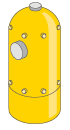
2 Synthesis
Synthesis gas is fed through a reactor and converted into a liquid called syncrude
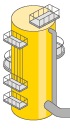
3 Hydrocracking
Syncrude is fed into a hydrocracker to break down molecules and form new ones
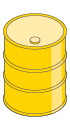
4 GTL products
The new molecules are distilled into GTL products, including PurePlus Technology base oil